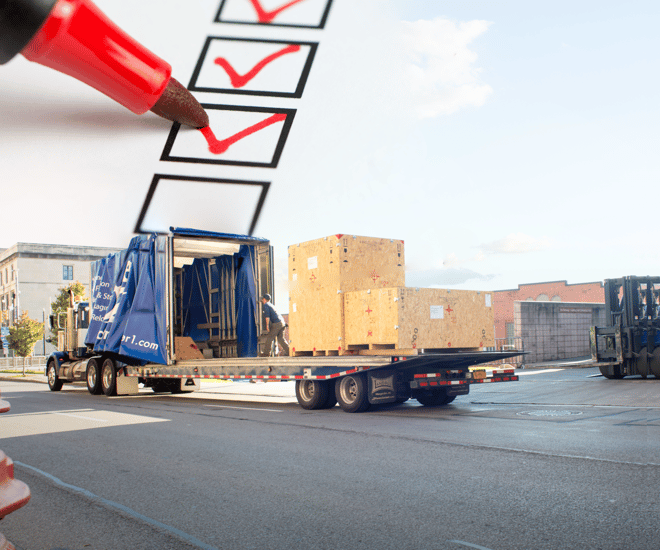
Every relocation, no matter how big or small, has its own set of unique challenges. Between dismantling machinery to everyday logistics, it’s important to have a plan in place for a seamless transition.
In this post, learn how to plan for a successful relocation for your manufacturing facility.
Overview:
- Communicate with employees, investors, customers
- Identify your subcontractors
- Prepare the new layout
- Adjust operations
- Audit your equipment
- Final review
Communicate with employees, investors, and customers
Transparency is key when planning a relocation. Throughout the entire process, your employees, investors, and customers should be well informed.
- Host a company-wide meeting or inform employees and investors through internal notices of the upcoming relocation.
- Establish a moving committee to keep department heads involved.
- Coordinate with departments on moving dates if the relocation is staggered.
- Make sure employees are aware of the new facility layout and if this affects their current workflow.
- Give customers adequate notice of the address change. Project updates should be frequently communicated to customers through emails and social media posts.
Identify your subcontractors
Depending on the scale of your project, your subcontractors may include engineers, machinery movers, electricians, pipefitters, and crating specialists.
- Provide detailed drawings of the old and new manufacturing plants to avoid confusion and delays.
- When selecting companies, make sure they are experienced and have the correct insurance in case of any issues.
- Avoid equipment mishandling and unsafe moving conditions by using a professional industrial mover.
Prepare the new layout
When planning the new layout, keep efficiency in mind. Equipment and workstations should be strategically placed to remove friction from your workflow.
- Create accurate and detailed layout drawings of the new facility. In addition to machine placement, be sure to include dock doors, pathways, utilities, and overhead equipment.
- Provide plans to the contractors to ensure equipment is properly placed and electrical and mechanical requirements are addressed.
Adjust operations
No matter how much planning goes into an industrial relocation, there will inevitably be disruptions to operations. Adjusting your supply chain to accommodate changes and keeping your customers informed of possible delays will mitigate issues during the move.
- Keep downtime minimal by moving equipment in phases.
- Provide employees with detailed work instructions.
- Have employees work in other areas while their department is being relocated.
- Inform customers that delays may occur during the move.
Audit your equipment
A review of inventory will determine which pieces will be moving to the new facility and if any unused equipment will be sold or go to scrap.
- Assess and document equipment including all dimensions, spare parts, accessories, and technical details before relocation.
- Attach manuals, maintenance records, spare parts, and accessories to the piece of machinery.
- Once placed, equipment should be tested to make sure nothing was damaged during the move. Equipment commissioning also helps identify areas of inefficiency in the layout.
Final Review
Now that you’ve successfully moved into the new space, it’s time to knock out those final details on the factory relocation checklist.
- Ensure employees have badges or keys to the new facility.
- Have your IT department set up computers and transfer phone lines.
- Update the company website(s), employee email signatures, business cards, and mailers with the new address.
- Issue emails and press releases to inform of the address change.
- Invite customers, local officials, and employees to a celebration event.
Conclusion
Plant relocations are no easy task but with proper planning and the right tools in place, your manufacturing facility can be up and running again with little downtime.
If you’re in the market for a plant relocation expert, contact Boulter today. Our extensive capabilities will help streamline your relocation project while saving you valuable time and money.
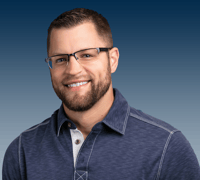
Ryan joined the Boulter team in 2016 as a field employee before transitioning to Packaging Shop Supervisor and now Project Manager. With his diverse background in the field and the crating and packaging shop, he is well-equipped to handle the complexities and challenges that come with managing projects of varying scales and requirements.