Easing Labor Challenges with Outsourced Maintenance

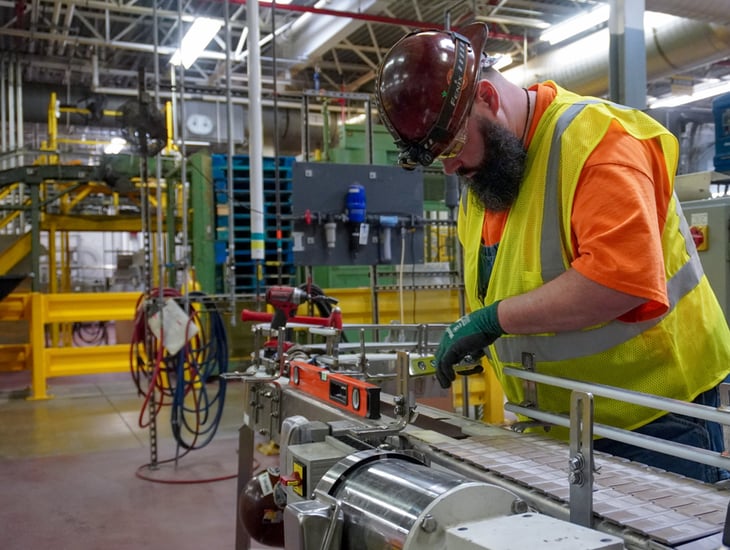
If you're hiring manufacturing maintenance technicians, you understand how difficult it can be to fill these critical labor gaps. The current labor market heavily favors employees, giving them more options and bargaining power than ever before. Even if you’re among the fortunate few with a maintenance team in place, challenges like employee burnout, human error, and the constant focus on emergency repairs often leave little time for proactive planning or strategic improvements to your plant. It can feel like every repair moves you one step forward, only to have unexpected equipment failures push you two steps back.
You’re not alone in facing these challenges, and there’s support available. Partnering with an outside maintenance contractor can extend your team’s capabilities without the added overhead. Learn how outsourcing maintenance can benefit your operation and help you regain control of your time, your team, and your budget.
Maintenance teams when the equipment breaks faster than they can fix it.
Maintenance Teams: Fighting Fires Instead of Preventing Them
It’s a familiar story: maintenance teams working harder and faster on equipment repairs only for another piece of equipment to break down the line. The endless cycle of emergency fixes and deferred preventative maintenance leaves little room for strategic improvements. By the time one problem is patched up, another pops up, and the domino effect begins.
Preventative maintenance flips this script. Instead of playing defense, you gain the ability to be proactive—to stop breakdowns before they start. It’s like putting out the fire before it has a chance to ignite. Partnering with an outsourced maintenance contractor, whether for scheduled shutdowns, emergency repairs, or long-term labor loans, enables your team to focus on strategic initiatives that have been sidelined.
How Outsourcing Maintenance Addresses Labor Shortages
Labor shortages are a common struggle in the manufacturing industry, and maintenance teams often bear the brunt of these gaps. Outsourcing maintenance offers a practical solution to alleviate these challenges in several ways:
- Filling Skill Gaps: Hiring and retaining highly skilled technicians is increasingly difficult. By supplementing your maintenance team, you get immediate access to a pool of experienced professionals who can handle complex systems and equipment without additional training.
- Scaling Up Quickly: When production demands increase or your in-house team is stretched thin, working with a maintenance contractor allows you to scale up your capabilities quickly. This ensures your operations don’t falter during peak periods or emergencies.
- Reducing Turnover Impact: High employee turnover disrupts workflows and creates knowledge gaps. An outsourced partner provides stability, allowing your facility to maintain consistent performance even when in-house staff changes.
- Boosting Team Efficiency: By supplementing your in-house team, outsourced professionals take on the heavy lifting of routine maintenance and repairs. This frees up your team to focus on strategic improvements, reducing stress and preventing burnout.
- Avoiding Costly Downtime: Labor shortages can lead to delays in addressing maintenance issues, increasing the risk of unplanned downtime. When you work with skilled maintenance techs you get the peace of mind that maintenance tasks will be completed on time, keeping your plant running smoothly.
How Outsourcing Maintenance Saves Money
You might assume that hiring someone to help with maintenance tasks is more expensive upfront—and that could be true in the short term. However, the long-term savings far outweigh the initial cost. Yes, outsourcing reduces the direct costs of training, salaries, and benefits for additional in-house staff. But the savings go deeper.
- Lower Training Costs: Hiring and training new employees is expensive, especially in a tight labor market where skilled technicians are hard to find. Outsourced maintenance teams come pre-equipped with expertise, eliminating the need for costly onboarding and skill development.
- Burnout Prevention: Short-staffed teams lead to overworked employees, and overworked employees make mistakes. Mistakes that cost money. An outsourced partner supplements your existing team, spreading the workload and reducing stress-induced errors.
- Early Issue Detection: More eyes mean more opportunities to catch problems early. An outsourced team’s specialized experience often uncovers potential issues your in-house team might overlook, preventing minor problems from turning into major, costly disruptions.
How Outsourcing Maintenance Improves Safety
Safety isn’t just a checkbox—it’s the foundation of a productive operation. An outsourced maintenance partner prioritizes safety by implementing proactive maintenance practices, conducting regular inspections, and addressing hazards before they escalate. Here’s how outsourcing helps you maintain a safer plant:
- Risk Reduction: When you rely on professionals for scheduled shutdowns or emergency repairs, you reduce the likelihood of accidents caused by rushed or incomplete fixes. A stable and experienced team ensures that safety protocols are followed rigorously.
- Burnout Mitigation: An overworked team is a dangerous team. Supplementing your staff with outsourced professionals alleviates the workload, reducing stress and fatigue that can lead to accidents.
- Turnover Stability: Employee turnover doesn’t just disrupt operations; it disrupts safety. Outsourced teams bring consistency and reliability, eliminating the risk of losing critical safety knowledge when employees leave or retire.
- Comprehensive Inspections: During scheduled shutdowns, outsourced teams conduct thorough inspections to identify hazards or maintenance needs. Addressing these proactively minimizes the chance of accidents and unplanned downtime in the future.
How to Select the Right Maintenance Contractor
Not all maintenance contractors are created equal. Selecting the right partner can make or break your outsourcing strategy. Here’s what to look for:
- Industry Expertise: Choose a contractor with a proven track record in your specific industry. Their familiarity with your equipment and processes will ensure they’re ready to hit the ground running.
- Flexibility: Your needs will change—sometimes day to day. Whether you’re scaling up during peak production periods or addressing specialized projects, your contractor should adapt seamlessly to your requirements.
- Preventative Maintenance Consulting: Some contractors go beyond just the repairs, offering line assessments to identify potential issues before they cause downtime. This service is particularly valuable for smaller facilities without the resources for a dedicated preventative maintenance program.
- Safety Mindset: A strong safety culture is non-negotiable. Ensure your contractor follows industry best practices and demonstrates a commitment to maintaining a secure work environment for everyone on site.
The Bottom Line
Preventative maintenance is key to navigating labor challenges, saving money, and ensuring the safety and efficiency of your operations. And outsourcing these tasks isn’t a stopgap solution; it’s a strategic move that allows you to focus on what you do best: running your manufacturing operation.
So why wait? Take the first step toward smarter, safer, and more cost-effective maintenance today. Your team will thank you, your budget will thank you, and your equipment will, too.
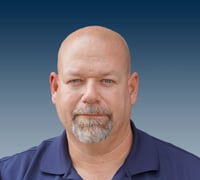
Jeremy is a third-generation millwright with over 30 years of field experience, managing some of Boulter's most significant and challenging projects. In 2024, he transitioned to the role of Project Manager, where he now applies his extensive expertise to ensure the successful execution of complex projects from start to finish.